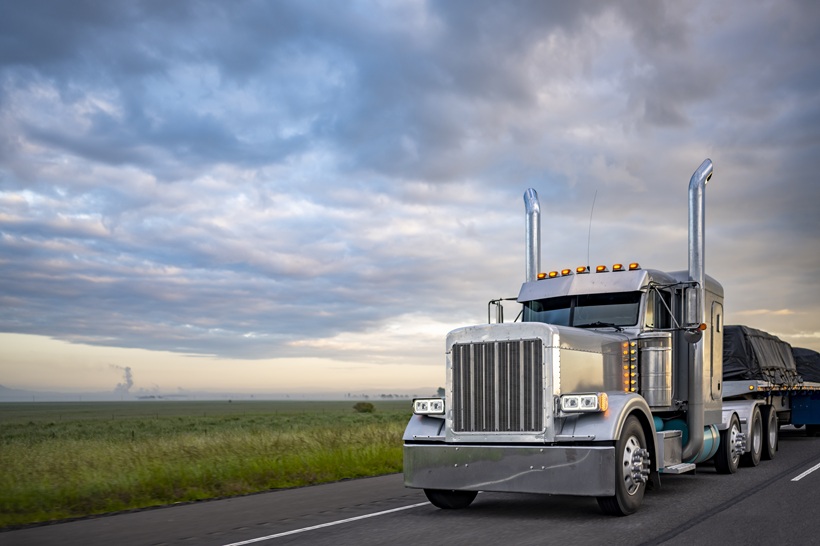
How to Avoid Costly Mistakes When Extending Asset Life Cycles
The calculus for Class 8 truck replacement has shifted in 2025. As recently as last year, industry consensus pointed toward a massive prebuy surge ahead of EPA emissions regulations taking effect on new equipment in 2027. Fleet managers were anticipating $20,000-$25,000 cost increases per unit, with analysts at ACT Research predicting potentially the largest Class 8 prebuy in history.
That scenario evaporated in March 2025 when the EPA under the second Trump administration announced a comprehensive review of 2027 Clean Truck regulations, effectively signaling their rollback or reversal. The urgency for prebuy has effectively disappeared overnight.
Cash flow constraints meet regulatory relief
The timing of this regulatory shift coincides with market conditions that make the prebuy cancellation particularly significant for fleet operators. Carrier profitability has reached generational lows, with Q1 2025 profit margins matching the worst performance since Q1 2010, according to aggregated data from publicly traded truckload carriers. Kenny Vieth, president of ACT Research, notes that the freight market downturn has now extended into its 13th quarter—nearly double the typical six-to-eight quarter cycle.
In a market where cash flow and capital availability are at a premium, this regulatory shift means fewer fleets will be purchasing new trucks in the near term. While this development will help balance sheets at carriers and dual-authority outfits of all sizes and freight types, it introduces a different set of operational risks that fleet managers must now navigate strategically.
Extended lifecycles by default
The absence of prebuy pressure doesn’t eliminate the underlying factors that make aging equipment increasingly expensive to operate—it simply changes the timeline and urgency around addressing these issues.
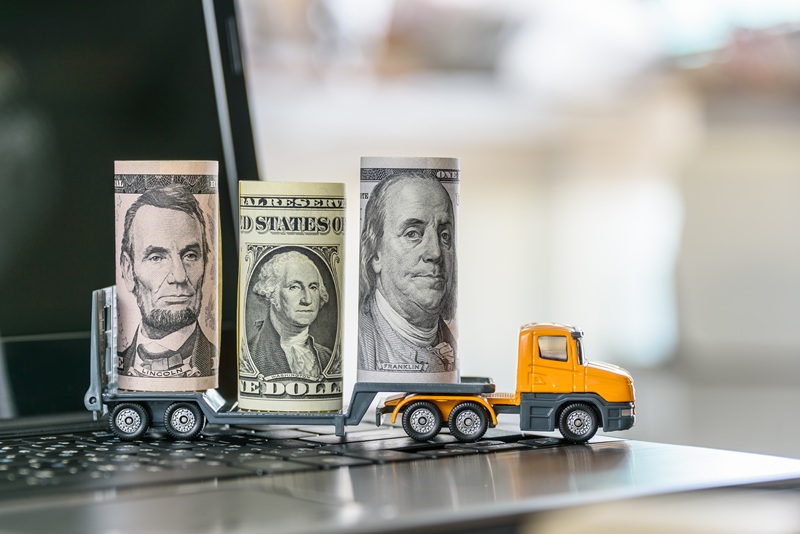
The implications extend beyond individual fleet decisions. As American Transportation Research Institute (ATRI) reports show, maintenance costs for vehicles aged 4-6 years now run 2.75 times higher than trucks under three years old, while breakdown intervals average just 37,700 miles between failures or unscheduled maintenance. These operational realities have become more relevant as fleets extend equipment lifecycles without the capital relief that new truck purchases might have provided.
This blog examines four tools fleets can take advantage of to prevent major maintenance setbacks that hurt the bottom line.
1. Proactive monitoring
Keeping older trucks on the road without costly breakdowns means catching small issues long before they become big problems. Today’s predictive analytics platforms sift through telematics, diagnostic codes, and maintenance logs to spot subtle warning signs weeks in advance. Fleets that have embraced these insights report up to 70% fewer unexpected failures and a 30% drop in repair bills.
For aging equipment, targeted monitoring is crucial. That means:
- Engine health checks: Watch for shifts in fuel efficiency, oil pressure, or temperature spikes that signal early wear.
- Emissions system care: Scan sensors and particulate filters to head off compliance failures.
- Suspension and vibration tracking: Identify imbalance or worn bushings before they damage axles or steering components.
- Safety systems audits: Regularly verify ABS, lane departure warnings, and collision mitigation systems to keep drivers and regulators happy.
Rather than sticking to calendar-based service intervals, many fleets now trigger maintenance by real-world usage. Telematics data can flag when a truck has logged its typical workload, ensuring you only service it when it genuinely needs attention.
2. Automated notifications
A good Computerized Maintenance Management System (CMMS) platform ties your whole maintenance workflow together, generating work orders and reminders exactly when vehicles reach key thresholds. For older trucks, you can configure alerts that go beyond standard checks and prompt in-depth inspections aligned with wear patterns that are unique to extended-service assets.
These alerts deliver a full health snapshot: recent fault codes, upcoming service recommendations, and mileage trends. By supplying that information straight to your planners and technicians, you eliminate chase downs, manual scheduling errors, and service delays.
3. Strategic cost optimization
Stretching a truck’s life means managing every dollar spent on upkeep. The best, most cost-effective fleets build a complete cost-of-ownership model, tracking repair frequency, parts prices, downtime impacts, and even opportunity costs from missed loads.
When you overlay data with real-time performance metrics, replacement decisions become surgical rather than guesswork. Instead of swapping trucks out after an arbitrary threshold, you retire or reinvest in units based on a clear picture of their remaining value. Integrating telematics, AI analytics, and digital diagnostics into one unified dashboard ensures you never miss a trend that could eat into your bottom line.
Preventive routines also get an optimized facelift: structured walkaround checklists, digital signoffs on brake and fluid inspections, and formal approval gates for major overhauls. These guardrails help you compare the cost of a heavy repair against the truck’s salvage value, so you only greenlight work that genuinely extends service life.
4. Risk mitigation frameworks
Aging fleets face risks like surprise breakdowns, regulatory consequences, and rising insurance premiums. Building a risk matrix for maintenance history, compliance standing, and failure likelihood lets fleets prioritize replacements before problems snowball.
Financial missteps often come from underfunding lifecycle reserves as carriers struggle with timing bigticket repairs or buyout decisions in volatile markets. By setting clear intervention triggers (for example, when annual repair costs exceed 15-20% of a truck’s replacement value), you protect cash flow and avoid crisis spending.
Finally, remember that technology alone isn’t a silver bullet. The best outcomes unfold when data-driven insights coordinate with strong vendor partnerships, including national service networks, volume discounts, and standardized protocols that guarantee consistent service quality. Marry that with disciplined financial planning and you’ll keep extended-life trucks running reliably, safely, and profitably for miles to come.
TL;DR
With the EPA’s 2027 truck emissions rules under review and fleet profitability at historic lows, many carriers are holding off on new equipment purchases and running older trucks longer by default. But extending asset life cycles comes with risks, including higher maintenance costs, increased breakdowns, and compliance challenges.
Fleets should embrace proactive monitoring, automated maintenance alerts, optimized costs with real-time data, and risk mitigation frameworks. By combining predictive analytics, strong vendor partnerships, and disciplined financial planning, fleets can keep aging equipment on the road without sacrificing safety or efficiency.